The development for blow molding machine
Blow molding is a plastic process where a thermoplastic resin is heated to its forming temperature, at material melting point it is made to form a hollow tube called parison or preform. In the beverage packaging industry, blow molding process is more widely used, and many plastic bottles are produced through the technology.
The heated plastic material is placed between two femal molds that are cooled by some medium. The blow molds close on the heated parison or preform and a gas, usually air enters via an open end of the plastic prefom via a blow pin or needle. The gas is flown into the closed female mold halves, to take the shape of the internal female closed mold, to make the bottle preform blow up to bottle. The bottle mold are then separeated and the cooled, bottle is allowed to drop out and repeat.
Over 100 years ago, to blow mold hollow objects, two sheets of cellulose nitrate were clamped between two female mold halves. Steam injected to soften the material, seal female mold halves and stretch the heated sheets to form the inside shape. But the high flammability of cellulose nitrate limited the usefulness of this technology.
In the early 1930s, more suitable materials, such as cellulose acetate and polystyrene(PS) come into the world. Unfortunately, because of the high cost and poor performance, limites the process.Finally, in the early 1950s, high density polyethylene(HDPE) was devloped and now blow molding is the largest user of HDPE, which is the largest volume thermoplastic produced in the world.
Now, most thermoplastic resins are suitable for plastic bottle blowing mould. Naturally, several are the leaders. In the year of 2000, HDPE is over 57% for blow molding marketing and PET follows with 33% market. So these two plastic resins are used over 90% of the blow-molding industry. All the other thermoplastic resins such as PP, PS, PVC…all combine for other uses in the approximate 10% blow-molded industry.
Regularly, the choice of material used is on the basis of performance, cost, barrier, availability,cleanliness, processing, transparency and strength. In the rapid growing markets at present are the automotive gasoline tanks, the 55-gallon drums(both HDPE) and the 20-oz soft drink products, the pint milk bottle(both PET), and the beer market is just starting with specialty marketing.
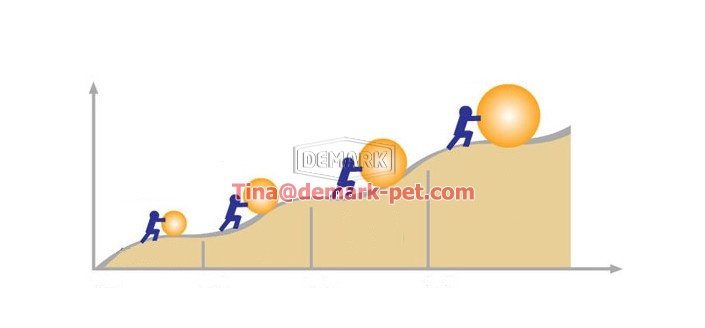
You may also like:
- advantage of auto blow molding machine
Today a Ghana customer comes to our factory to discuss the features of auto blow molding machine he prefer. Such as: 1. For seperate control of power for different par...
- bottle blow molding machine type
There are two kinds of bottle blowing molding machine in the world: one is INJECTION STRETCH BLOW MOLDING MACHINE (one step – injection and blowing are in one machine ), anoth...
- Three kinds of blow molding machine
For blow molding machine area, three kinds of blow molding machine take over the market: injection blow molding, extrusion blow molding, and stretch blow molding. Regula...
- How to choose a PET bottle blow molding machine?
How to buying a blow moulding machine can be a nerve racking experience for the fresh entrepreneurs. The PET bottle blow molding machine price is a secondary consideration. There countl...
- Blow molding process VS injection molding process
Blow molding a very popular manufacturing process which widely used in liquid packaging, such as plastic bottle, mineral water bottles, cosmetic bottles, drink bottles, plastic jug, pla...
Notice: The views expressed are my own and do not necessarily represent the views of DEMARK.
Copyright © 2013 - 2024 www.pet-machinery.com all rights reserved. Designed by Tina | Sitemap